This article was first published by Oliver Wyman here.
The goal of full warehouse automation might soon be in sight, at least for some.
The idea of automating the warehouse is almost as old as logistics and supply chain management itself. The prime motivation of automation is to increase warehouse productivity and profitability while improving overall efficiency in operations by eliminating human error. Rising labor costs, the challenges of constructing and operating warehouses in highly compact footprints in inner urban areas, and safety and environmental concerns have all fueled continued investment in increased levels of warehouse automation. That journey is now closing in on its end vision for a fully autonomous warehouse that can operate 24/7.
Where automation is today
Most warehouses have now automated at least part of their operation. Retailers and fast-moving consumer goods (FMCG) companies often touch level 4 autonomy – where no human intervention is required – for at least some part of their operation. Warehouses at the leading edge deploy advanced hardware and software, where several hundred smart robots are deployed in the warehouse to store and pick goods in a complex, three-dimensional bin system.
It would be incorrect to assume that this level of automation has been achieved in all industries, however. The challenges of warehouse automation are specific to the industry. (See Exhibit 1.) Not only does the current level of automation vary greatly by industry but it can also vary even within the business. For instance, while carmakers and tier-1 suppliers often achieve high levels of automation in picking small components using fully automated systems that shuttle between store locations, these same businesses manage a much lower level of automation when having to handle a component portfolio that varies in size and weight.
As a rule of thumb, it holds true that the larger the item and the more diverse the product portfolio in terms of volume or weight, the more difficult end-to-end warehouse automation becomes.
Exhibit 1: Characteristic levels of warehouse automation by industry
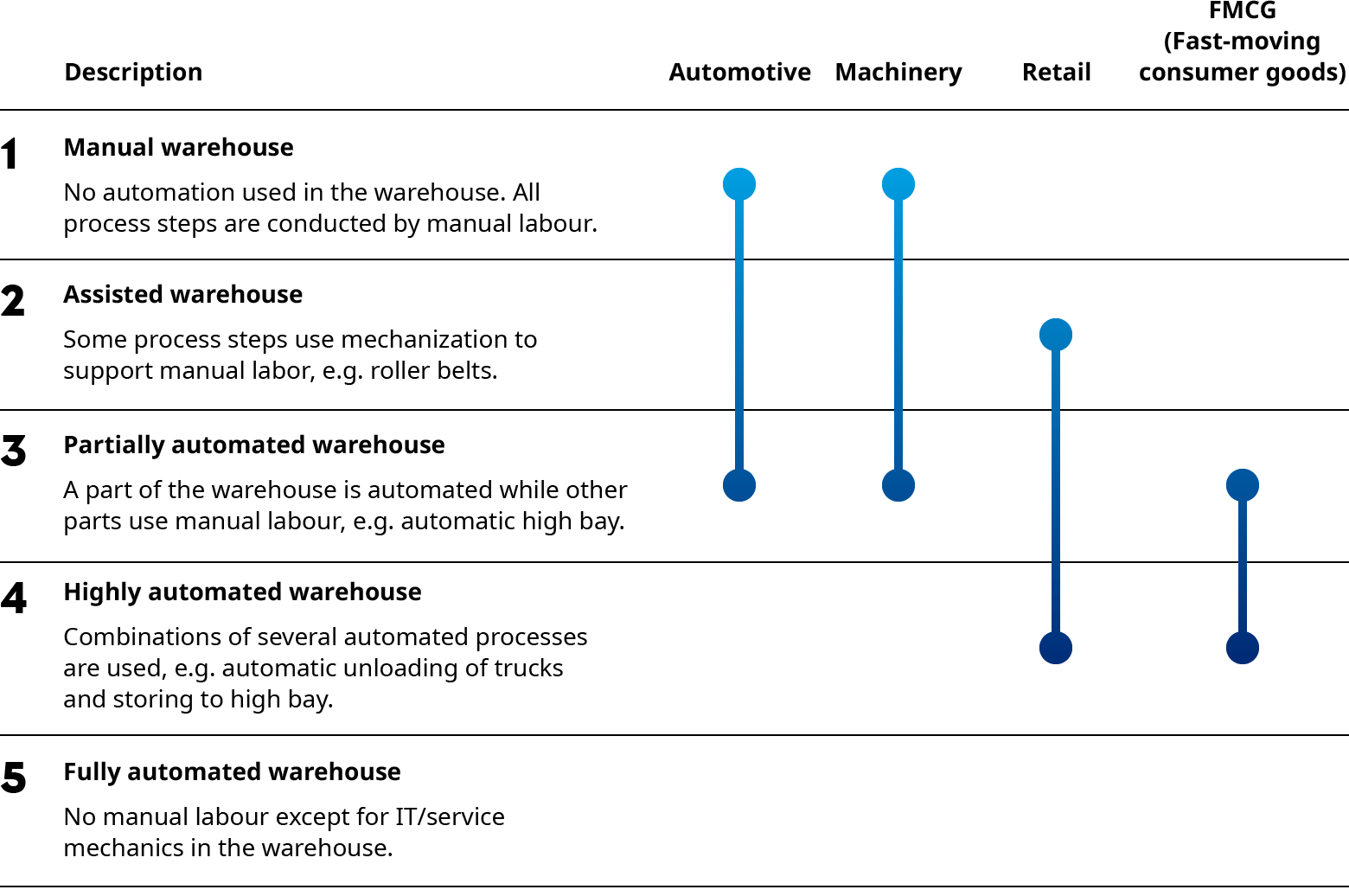
Source: Oliver Wyman analysis
Challenges on the road to full automation
Many solutions are now available “off the shelf”. The technology and systems needed to move a pallet automatically from a truck onto a conveyor and then into the storage warehouse in one seamless movement, one that then merges into automatic pallet storage within the warehouse, are readily available. The decreasing price of sensors, e-labels and machine vision systems ensure that the robots, automated machines and the various components of the automated system are all able to communicate with each other seamlessly.
The biggest challenge now facing warehouse operations is that many of these hardware and software solutions are in effect “islands” – and there is no easy way to connect these islands to create a system that is fully autonomous. This is true especially for warehouses where the automation system has evolved over time, a situation more typical than not in most companies. The legacy of piecemeal acquisition ensures that it will inevitably be a major struggle to connect the patchwork of hardware, software, and IT-architecture solutions. This is a challenge full automation has to tackle. Thereby, it is of paramount importance for companies to develop digital supply chain capabilities, where not only the right hard- and software is required but also the right people and an organization that is capable of implementing and maintaining this setup.
A second important issue is data: Poor data quality or data incompatibility can be the undoing of even the best of automation systems. Connectivity and data are the equivalent of the blood and the cardiovascular system of the autonomous warehouse. The hard truth is that almost all companies today struggle with getting their data right. At every step in the supply chain, it is essential to have accurate, real-time data, including for packing specifications and lot sizes. The data has to be exact in order to enable the machine intelligence to decide how to handle the various items.
Getting automation right
Compared to a conventional warehouse, a fully autonomous warehouse is more akin to a machine for production rather than being just a place for storage. Ensuring that the autonomous warehouse functions as desired requires the company to think afresh about the role of the warehouse itself – and link seamlessly into all adjacent processes. If the benefits of the autonomous warehouse are to be fully realized, it is necessary for the company to think about reshaping their operating model and accompanying organization, including the processes and IT systems, in order to ensure that they are all fully integrated.
These challenges can make the strategy, design and implementation of warehouse automation appear particularly daunting, especially for large corporations, such as those in retail, automotive or manufacturing, that often have enormous warehousing footprints located at hundreds of different sites.
The place to start: tailoring automation to business and service requirements
The vision of full warehouse automation is big lure for many Chief Operating Officers (COOs). The benefits are transparent, enabling a significant performance edge and future cost benefits. Yet full automation might not be desirable in all circumstances given the current state of technology. Depending on the industry, partial automation might well yield a more optimal outcome. To establish whether full automation is the right goal for the business requires developing a full understanding of the company’s business and service requirements.
Customer and service requirements vary significantly between markets, customer segments and product groups. Rather than a one-size-fits-all approach, leading players follow a segmented approach to warehouse automation, tailoring their warehouse designs to the specific needs of individual channels, categories, and order profiles. They are careful to choose the right level of automation and the right technology for each of their segments, ensuring that what is implemented is able to provide the required degree of flexibility for a large spread of order profiles, fulfillment speeds, and scalability.
The answer to warehouse automation is more often than not to adopt a tailored approach, one located in the specific service requirements of the company. By thinking of the warehouse automation challenge in this way, the COO is able to start determining the most appropriate automation strategy for the company. Done right, this will set the road to full autonomy.